Implementing Quality Control in Construction Projects: Best Practices
Understanding Quality Control in Construction
Quality control in construction is essential for ensuring that projects meet both regulatory standards and client expectations. It involves a series of processes designed to guarantee that materials, workmanship, and finished structures adhere to specified requirements. Without effective quality control measures, construction projects can suffer from defects, delays, and increased costs.
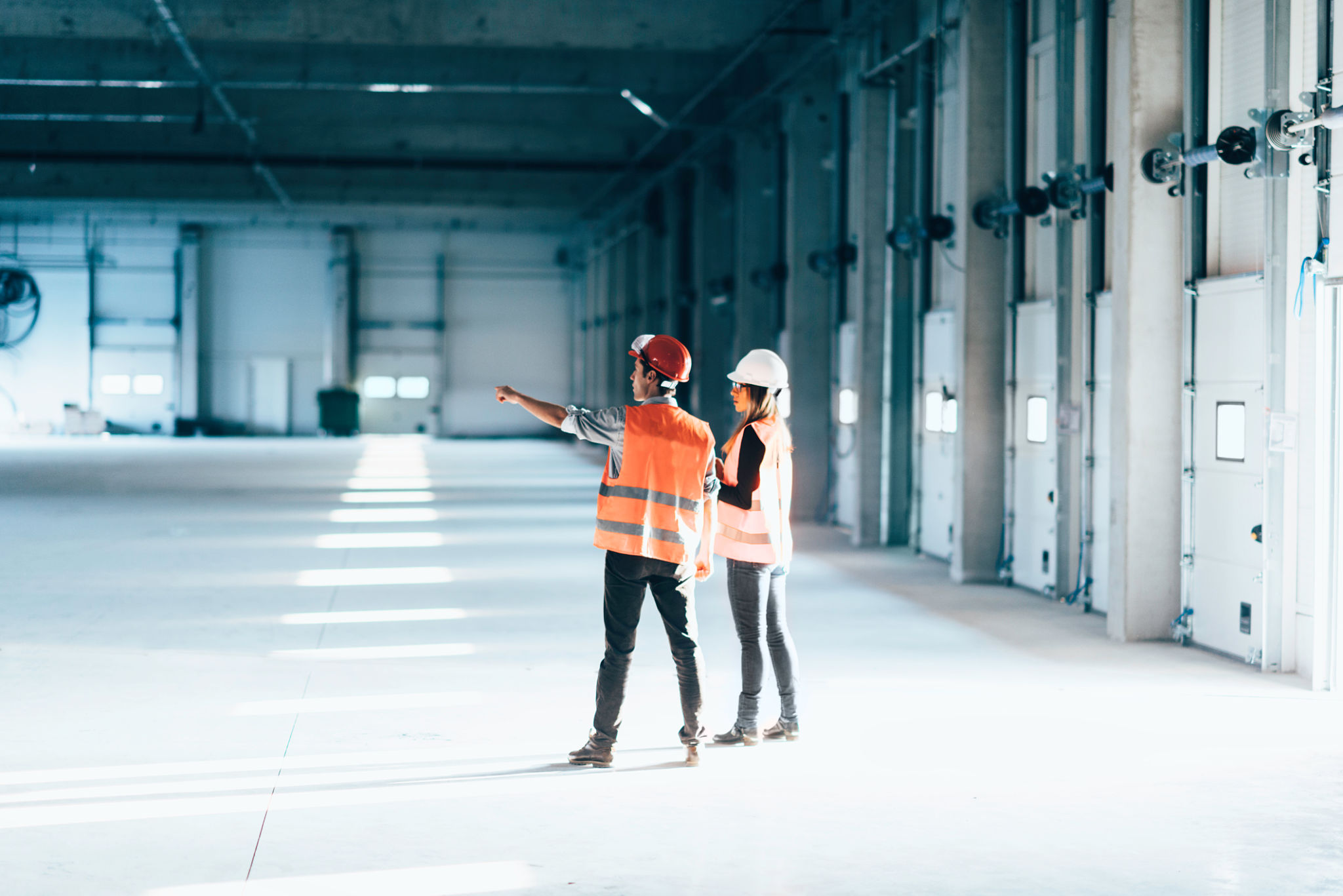
Implementing a robust quality control system starts with clear documentation and communication. Establishing comprehensive guidelines and checklists can help construction teams understand what is expected at every phase of the project. This documentation should cover everything from material specifications to safety standards, ensuring that all team members are on the same page.
Creating a Quality Control Plan
A well-defined quality control plan is a cornerstone of successful construction projects. This plan should outline the scope of work, define roles and responsibilities, and establish procedures for inspections and testing. Key elements of a quality control plan include:
- Project specifications and requirements
- Inspection schedules
- Testing methodologies
- Documentation procedures
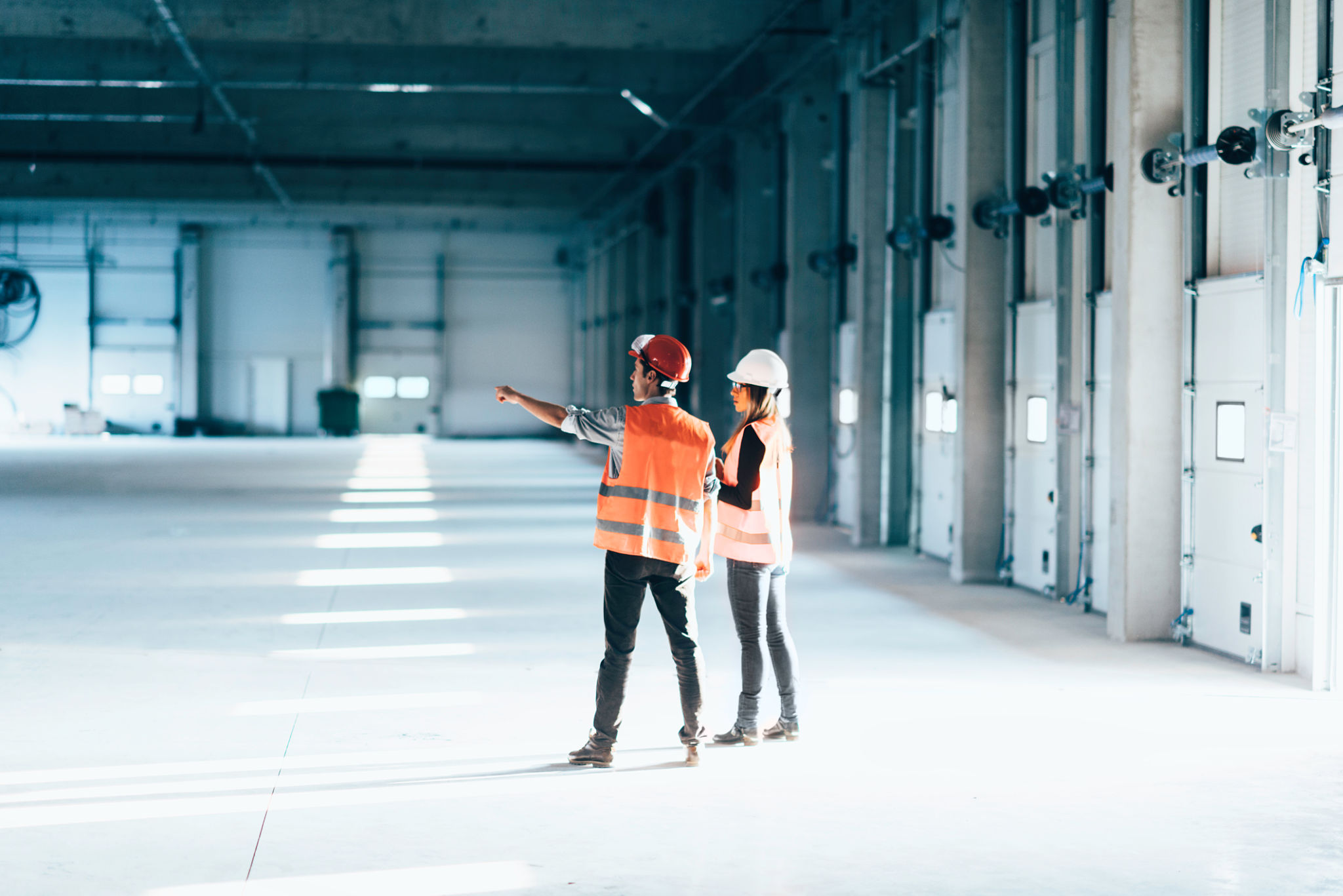
It's crucial to appoint a dedicated quality manager or team responsible for overseeing these processes. This team should have the authority to halt work if quality issues are identified, ensuring that problems are addressed before they escalate.
Implementing Regular Inspections
Regular inspections are vital for maintaining quality throughout a construction project. These inspections should be scheduled at critical phases of the project, such as during foundation work, structural framing, and final finishes. Inspections help identify potential issues early, allowing for timely corrections and minimizing costly rework.
In addition to internal inspections, it is beneficial to engage third-party inspectors who can provide an objective assessment of the project's quality. This independent verification adds an extra layer of assurance that the project meets all necessary standards and codes.

Utilizing Technology for Quality Control
Advancements in technology have revolutionized quality control in construction. Tools like Building Information Modeling (BIM), drones, and mobile inspection apps enable more efficient monitoring and management of construction quality. BIM allows for detailed visualization of projects, helping teams identify potential issues before they become problems on-site.
Drones provide aerial views of construction sites, offering a broader perspective that can reveal discrepancies not visible from the ground. Mobile inspection apps streamline the inspection process by allowing real-time data collection and reporting, making it easier to track progress and ensure compliance with quality standards.
Fostering a Culture of Quality
Finally, fostering a culture of quality within the construction team is crucial. This involves training workers on the importance of quality and how to achieve it through best practices. Encouraging open communication and feedback can also promote continuous improvement and reinforce the commitment to maintaining high standards.
The benefits of implementing effective quality control measures in construction projects are numerous. By prioritizing quality from the outset, companies can enhance their reputation, avoid costly errors, and deliver projects that satisfy both regulatory requirements and client expectations.